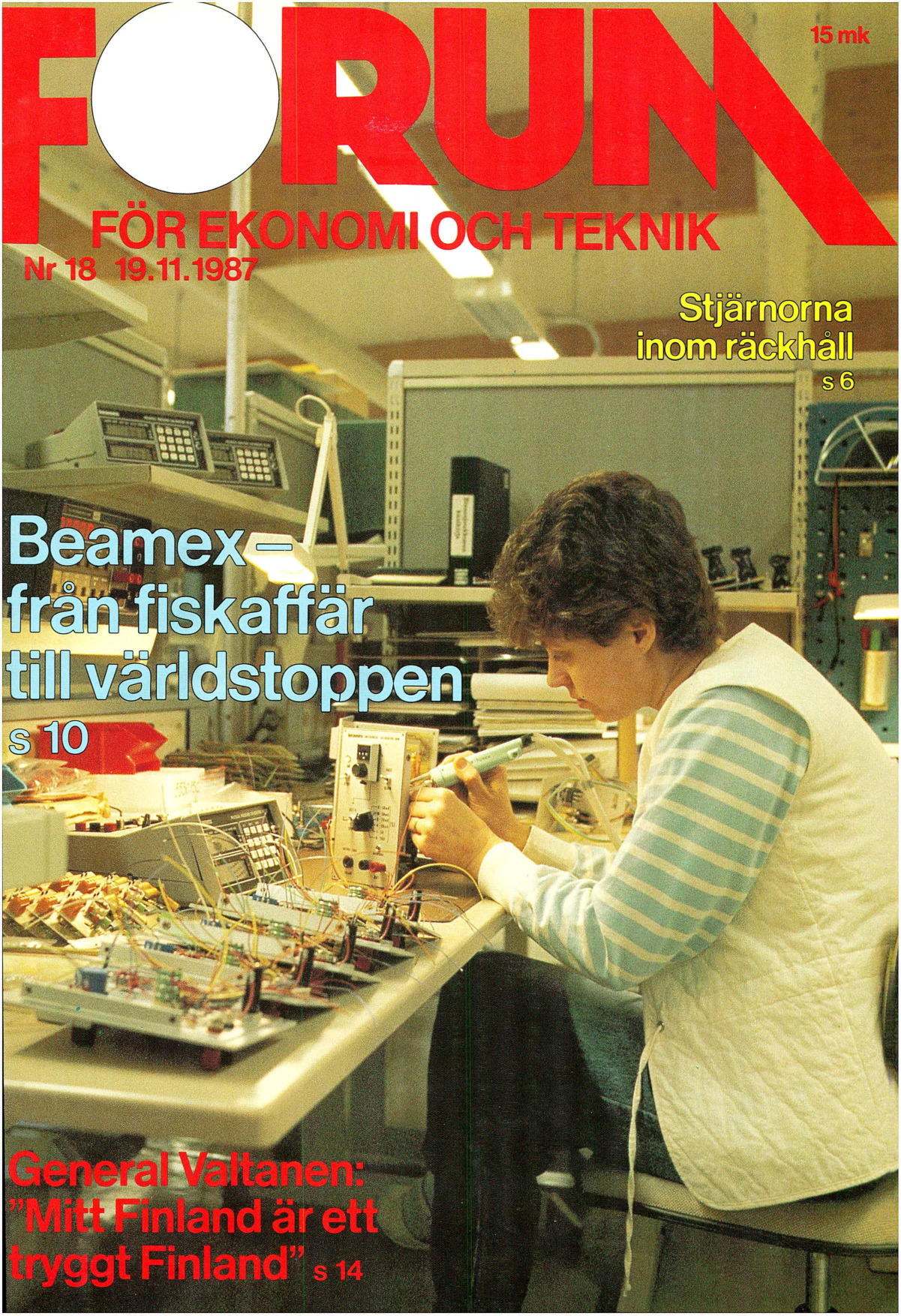
BMW i Regensburg
av Lars-Gunnar Larsson Forum 1987-18, sida 26-27, 19.11.1987
BMW i Regensburg: Logistik på fabrik skär kostnader
När den senaste för USA-export avsedda BMW-kärran i 3-serien börjar tillverkas, finns de passande bilsätena ännu inte inom väggarna i den nya fabriken i Regensburg. Men fem timmar senare behövs de. Fortfarande två timmar innan den blivande amerikanske bilägaren ska få sitt bilsäte ”har ingenting hänt”. Men då beställs det från underleverantören femton kilometer längre bort, Planeringsmiss, panikhandling, produktionsstopp ngalunda. Nu effektueras beställninge hos underleverantören Schmitz & Co i
Bad Abbach. Exakt de säten som behövs ör denna och de kommande fjorton BMW3:orna stoppas i särskilda transportbehållare med möjlighet till automatisk lastning och lossning. Upp med dem på lastbil, färd ill Regensburg, dit de når fram tjugo minuter före deadline. Och via förarlösa, indukivt styrda truckar kan bilsätena majestäiskt glida fram i precis det önskade utförandet på den rätta punkten av manteringsbandet, vid precis rätt tidpunkt, Just In Time. För den utomstående betraktaren är det som kaninen som plockas fram ur trollkarens hatt: det verkar trolleri, men man vet ju att allt bygger på kalkyl.
Skillnaden är, att bilbyggaren i motsats ill magikern avslöjar bakgrunden till sitt ho 2 kuspokus. Att sitsmakarna i Bad Abbach klarar utleveransen av den begärda varan beror inte på att man plockar ur ett stort lager. Det sker istället genom en intensiv kontakt mellan biltillverkare och underleverantör. Fyra månader i förväg ger BMW sin produktionsplan till Schmitz, som på basen därav kan göra materialbeställningar. Tre veckor i förväg kommer — allt per datakontakt — en uppställning av vilka sätesvarianter i vilka olika utföranden som kommer att behövas. Fem dagar innan lämnar fabrikens montagestyrning besked om vilka fordonsnummer och därtill hörande utföranden av säten man bestämt sig för. Och den “beställning”, som kommer till Bad Abbach två timmar innan sätet sätts på plats i Regensburg, blir I normalfall bara en bekräftelse på vad man redan vet och jobbat efter.
Med ett kapacitetsstarkt internt optokabelnät och databärare bak på varje bil har de som styr BMW-produktionen hela tiden överblick över produktionslaget, i stort och smått,
Underleverantören kvitterar genom att per telekommunikativ väg sända ordersedeln samtidigt som lastbilen går iväg…
Sparar in arbetsplatser
Detta är det mest spektakulära exemplet på den stenhårda satsningen på logistik i BMW:s nyaste fabrik. Transport- och lagerkostnader är pressade till ett minimum. Detta har uppnåtts inte minst genom att underleverantörerna — bildlikt talat — mer eller mindre tvingats att placera sig vägg i vägg med bilfabriken. Vidare genom att automatisera tillförseln av delar till produktionen, och att hålla de nödvändiga mellanlagren på minimal nivå vad gäller volymen — och på låg nivå, dvs i markplan, vad gäller geografin.
BMW uppskattar, att logistikkonceptet i Regensburg sparat in 125 arbetsplatser i förhållande till traditionell fabriksdesign.
— Det finns inget liknande, inte i Japan heller, säger BMW-chefen Eberhard von Kuenheim självsäkert om sin nya fabrik.
Men vanligtvis brukar det senaste också vara det bästa. Och om BMW nu verkligen ligger främst — vilket sist och slutligen blir en trosfråga — så har man uppnått det ‘utan spektakulär insats av robotisering, som i exempelvis den människotomma hall 54 hos Volkswagen i Wolfsburg, eller monteringen av hela cockpiten genom vindrutan så som i den nya fabriken för Opel Omega.
Sanningen är förmodligen, att man inte ska jämföra äpplen och bananer. Genom hall 54 i Wolfsburg rullar dagligen 3 000 Goffar. BMW siktar i Regensburg på maximalt 500 fordon per dag.
Flexibilitet med datorisering
Ett bättre sätt att karakterisera BMWRegensburg är då förmodligen, att man är state of the art, när det gäller att ”på enklaste sätt bygga komplicerade bilar”. Dess grunduppgift är nämligen att säkert och smidigt klara ständiga växlingar mellan Europa- och USA-versioner, mellan standara, cabrio och fyrhjulsdrift och ett otal olika detaljutföranden. Detta ställer exceptionella krav på information och överblick.
Man bemästrar det med disciplin och datörisering. Varje bil löper igerom samma huvudled i den över tio hektar (580x200 meter) stora produktionshallen. Variationerna innebär, att man gör avstickare längs olika sidospår. Det ena interna transportsystemet avlöser det andra. Smärre buffertlager just vid dessa växelpunkter gör att man klarar mindre störningar. Förenandet av kaross å ena sidan, och dörrar, instrumentbräda samt motor-växellåda å den andra, sker på givna punkter. Okontrollerad utleverans kommer inte i fråga.
Längs hela fabriken löper en prestationsstark optokabel, mogen att hanter 18/1987 FORUN enorma mängder av digitaliserad information. Denna står i trådlös förbindelse med databärare, som finns bak på karosserna under deras färd mot fullbordande. Med identifikations- och styrningssystemet Premid från Philips har man I varje läge mikrooch makrokunskap om produktionsläget.
Detta system skapar också förutsättningar för bättre information till arbetaren på verkstadsgolvet, bättre kvalitet och säkerhet i det utförda arbetet: inom kort lämnar man via bildskärm upplysning till montören om vilka delar som ska monteras på bilen man håller på med.
”Rullande trottoarer”
Decentraliserad montering, automatisering och ergonomi är nyckelbegrepp i det interna transportsysternet. Här några problemlösningar: Under första delen av montagetiden åker karosserierna längs hängande banor, som medger höjning och sänkning samt vridning upp till 90 graders vinkel. Fördelen med det är att man kan undvika allt montagearbete med händerna sträckta uppåt. Produktionsbanden fungerar som rullande trottoarer. Arbetaren följer automatiskt med under arbetets gång.
Förarlösa truckar sörjer för leveranserna från mellantager till produktion. Endast för vissa delar, och till en början, sker fördelningen till oroduktionsbandet manuellt med gaffeltruckar. Efter lackeringen skruvas dörrarna loss och färdigmonteras för sig, fö att senare återförenas med den praktiskt taget färdiga bilen. Också instrumentbrädan färdigmontras i egen linje.
Automatiseringen innefattar också påfyllning av bränslen, bromsvätska och kylvatten, inläggning av reservhjul och klistring av tätningslister I dörrar. Motor och växellåda körs via en speciell bärram automatiskt på plats under bilen till fromma för ergonomin.
I slutmontaget tas bilen över av sk Chängen. Dessa ger optimal åtkomlighet. Varje hänge har en egen elektriska motor.
Men ännu är det inte dags att vrida om startnyckeln och känna den minsta ”körglädje”. Efter det att axlar och avgassystem monterats lämnas bilen automatiskt över på självkörande ”kälkar”, s k skids, på vilka de färdas genom ett område, som omfattar 300 testpunkter.
Motorstart i testkabin
Färden går i normalfall till den tredje och sista montageavdelningen, där konservering av lacken sker. Skulle något fel upptäckas eller motorn inte starta, övertas fordonet av en truck, som via induktivslinga hittar vägen till reparationshallen. Först i de slutna testkabinerna startas motorerna för första gången.
Den nya BMW-tfabriken är den tredje produktionsanläggningen för den sydtyska biltillverkaren, de övriga finns i Mönchen och i (också sydtyska) Dingolfing. Motorer kom 150 städer slogs om den nya BMW-fabriken, vinnare blev Regensburg, tio mil norr om BMW-staden Mönchen. Huvudbyggnaden på 580 x200 meter i centrum för det 142 hektar stora fabriksområdet.
mer från en egen fabrik i österrikiska Steyr, plastdetaljer från Landshut.
Fullt utbyggd, 1991, kommer fabriken att i två skift tillverka 400 bilar per dag. Ännu kör man med halva den produktionen i ett skift, vilket är lika med 1 900 anställda. Fullt utbyggd kommer fabriken att ha kostat arygt 3 miljarder FIM.
Regensburgfabriken är förberedd för långt mer high-tech än vad som idag — trots allt det ovannämnda — tillämpas, inte minst vad gäller den datorintegrerade produktionen, förkortat CIM. Den allmänna utvecklingen och de egna kalkylerna kommer att bestämma om och när denna slumrande potential också utnyttjas.
Lars-Gunnar Larsson €
FÖRENINGSBANKEN I FINLAND AB
Aktiva Finansieringstillgångar
Fordringar hos Finlands Bank… Fordringar hos andra inhemska
Fordringar hos utländska banker
Krediter till allmänheten
Betalningsförmedling ….
Resultatregleringa Övriga finansieringstillgångar. . .. Omsättningstillgångar
Masskuldebre Övriga omsättningstillgångar … Investeringstillgångar
Masskuldebrev
Fastigheter och fastighetsaktier Anläggningstillgångar
Fastigheter och fastighetsaktier . Maskiner och inventarier …. Leasingobjekt Övriga anläggningstillgångar . Utgifter
Koncernmånadsbalans den 30 september 1987 (miljoner mark)
Passiva
Främmande kapital 862 Checkräkninga 2231 Depositioner
Masskuldebrevslån .. 1774 Skulder till Finlands Ban 16 782 63 655
Skulder till andra inhemska banker och kreditinrättninga 2 620 Skulder till utländska banker . .
1924 Skulder till state 1143 Betalningsförmedling
Debenturlå 1990 Resultatregleringar . . 4 525 Övrigt främmande kapital Räntor och övriga inkomster ..
7073 Reserveringar 229 Minoritetsandel 806 Eget kapital
Aktiekapita 526 1255 502 1743
För Direktionen Mika Tiivola
FOÖRUN, 18/198 113 381
Ansvarsförbindelser
Kurt Stenval 498 Övrigt bundet eget kapital 3 242 Fritt eget kapita 113 381 26 75 milj. m milj. mk
För Förvaltningsrådet
Jaakko Honk 27
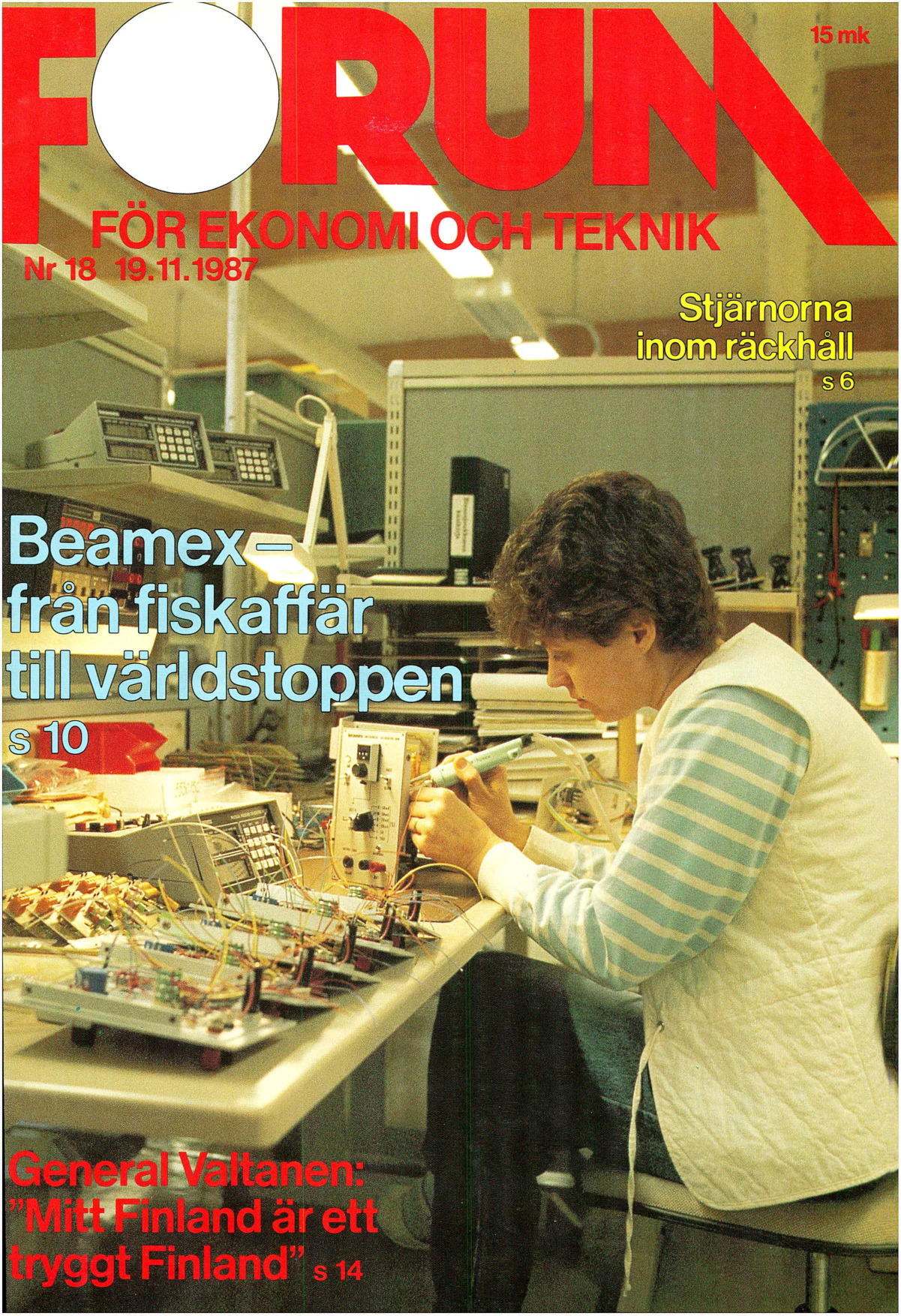