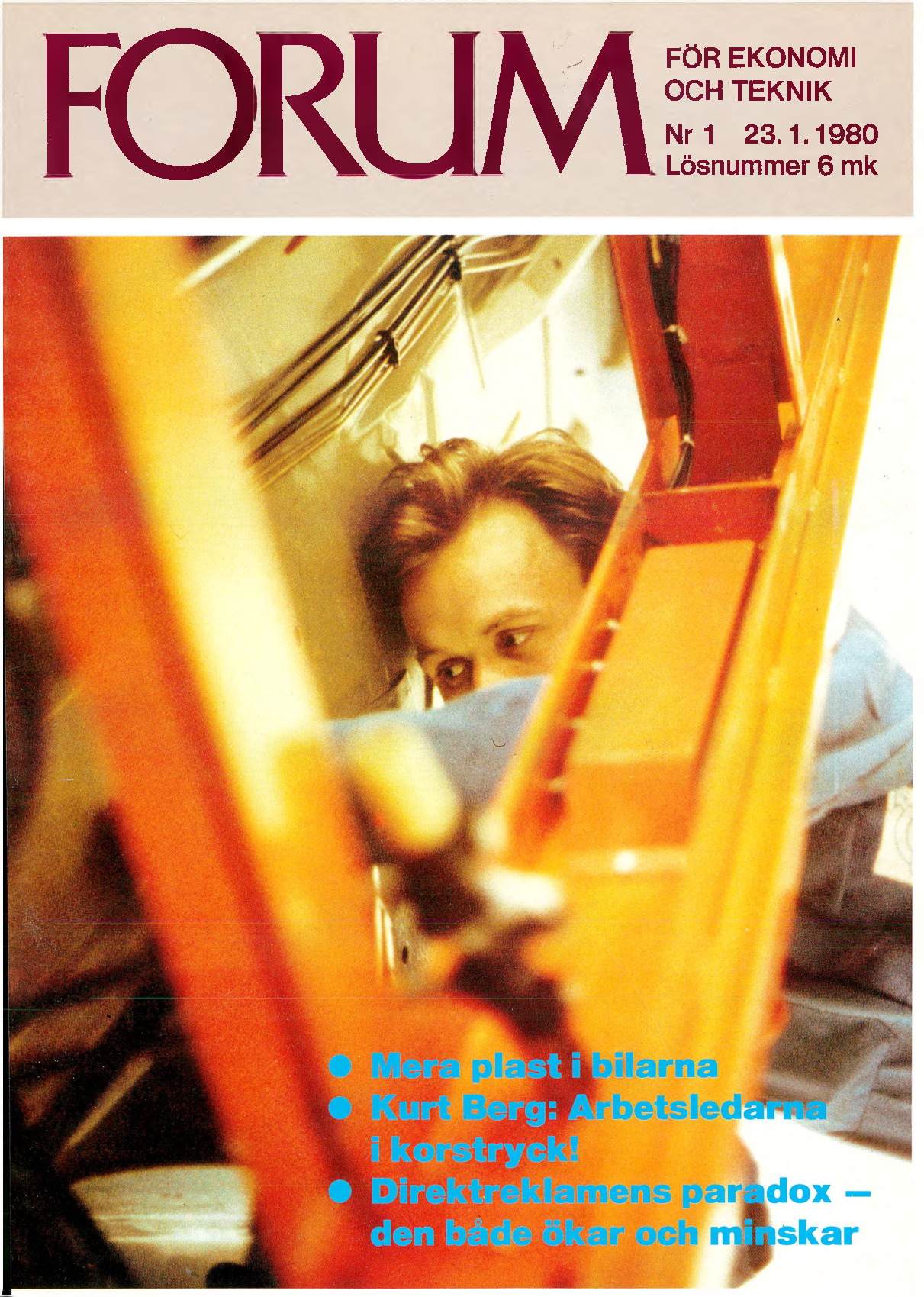
Mera plast i bilarna
av Kai Finell Forum 1980-01, sida 06-07, 23.01.1980
Mera plast i bilarna
I bilar har plast använts redan under ett kvartssekel, men hittills inte spelat någon större roll i bilindustrins råvarubudget. Smärre plastdetaljer har ofta varit ett medel att smått obemärkt sänka produktionskostnaderna, utan någo utåt synlig kvalitetsförsämring. Bränslekrisen har dock abrupt aktualiserat bruket av nya — ofta oarmerade — kvalitetsplaster också i ett flertal direkt vitala bilkomponenter. Men nu för att spara vikt — ibland rent av till priset a högre tillverkningskostnader.
NW” I fjol höll dr John D Young, chef för Automotive International Du Pont Co Plastic Products and Resins Department, ett uppmärksammat föredrag i Genåve inför brittiska Institute of Mechanical Engineers. Han framhöll bland annat att termoplasternas snabba frammarsch kommer att leda till en påfallande ökning av bilindustrins behov av PETP(polyethylene terephthalate)-polyesterhartser i många tidigare metalldominerade ingenjörstekniska = tillämpningar.
När allt kommer omkring behöver kanske inte amerikanska privatbilister pruta fullt så mycket på sin inrotade böjelse för bilar av stort format som pessimisternas framtidsspådomar antytt.
Från år 1955 har USA-bilens plastmängd ökat från i medeltal blygsamma 5 kg per bil till cirka 90 kg 1979. Nu räknar emellertid amerikanska bilkonstruktörer med en i år fördubblad plaståtgång, för att göra årsmodellerna 1980 kännbart lättare. Visst kunde man som motargument påpeka att också plasterna görs av olja, men därtill genmäler bilproducenterna, att plasterna väl kan göras av stenkol, vilket ju USA har gott om för århundraden framåt.
Även europeiska bilindustrin — med välkända Bayer-koncernen som forsknings- och utvecklingsstöd — säger sig nu vara inne på linjen att allt flere bilkomponenter som nu görs av metall snabbt måste ersättas med moderna plastmaterial.
Hela frontmasken på denna Chevrolet-modell är av plast gjuten i ett enda stycke.
Första ronden 400 kg
Viktminskningskampanjens förberedande rond är faktiskt redan över för USA-bilarnas del. ”Full-size”-modellerna har, genom flera olika åtgärder, blivit bortåt 400 kg lättare på några få år. Verkligt kännbara nya viktreduktioner har nu planerats för den kommande andra ronden, i avsikt att möta 1985 års hårt tillstramade bränsleekonominormer.
Denna andra omgång ska i själva verket mer domineras av viktnerskärning än någon påfallande krympning av USA-bilens format. Man gör allt för att i stort sett kunna bibehålla amerikanernas familjedimensionerade bil med rätt kraftig motor och bekväm kör- och sittkomfort ock så under långdistansfärder.
Konturerna måste dock ytterligare strömlinjeformas och ytorna genomgående befrias från virvelbindande yttre detaljer samt upphöjda dekoroch liknande lister. Tyvärr finns inte mycket kvar att tillämpa av den enkla viktminskningsregeln att helt sonika byta ut alla tänkbara tyngdre metalldelar mot lättare repliker av billig plast. Flera nya högvärdiga material måste fås fram.
Mekaniska system av plast
Hela så att säga funktionssystem måste utarbetas med blicken fäst på specialplaster som i flera avseenden har utpräglat metalliska egenskaper
FORUM 1/80
Strålkastarhus av plast är en relativt ny lösning.
allt igenom. Främst då seghet och styrka, samt hög värmetålighet och styvhet. Det är här som termoplastiska polyestrar och polykarbonater markant kommer in i bilden för personhilens utveckling mot lättare modeller. Likaså får konventionella armerade plaster i många fall vika för moderna kombinationer av allehanda formsprutade hartsmodifikationer. Du Pont ser med optimism fram mot de möjligheter som erbjuds av en mångfald PETP-baserade hartser. Visserligen däribland även en hel del modifikationer med hjälp av olika mineralier som tillsatsämnen samt glas och andra oorganiska additiver med både hög och låg molekylärvikt. I försöken att eliminera gjutskevningen hos formsprutade termoplastpjäser har redan anmärk ningsvärt uppmuntrande resulta nåtts vid PETP-experiment.
Mycket nytt redan i år
Bland annat en hel frontmask i ett enda stycke förefaller både lovande praktisk och tillräckligt hållfast. Men också smärre aktiva exteriördetaljer såsom separata strålkastarhus har gjutits med perfekt passning och förekommer redan i årets modeller.
Under marknadsföringsnamnet Rynite har Du Pont redan tidigare presenterat ett antal olika plastkombinat med mycket hög elektrisk genomslagshållfasthet och resistans så att materialet med framgång kan tilllämpas i strömfördelarhöljen samt andra kapslar och kåpor för bilens elutrustning.
Tack vare god mekanisk hållfast En specialkomponerad hålstansad polyesterelastrem th passande till ett ”knagg”drivhjul av Rynite 5320 i ett hölje av glasarmerad Zyton-nylonharts, samt drivblock och fönsterbåge av formsprutgjuten Delrin-acetaldehydharts. Viktbesparingen är rätt anspråkslös, men mekanismen möjliggör utrymmes besparande dörrdesign.
Ett exempel på PETP:s mångsidiga möjligheter är denna Du Pont-bild nedan av en detalj i termoplastharts — termoplasterna tränger ut de dyrare hård lättmetallerna på allt flera områden.
FORUM 1/80
Av Du Ponts Rynite är täckpanelen på bilden.
het och styvhet, visuellt tilltalande ytstruktur, konstanta gjutdimensioner med minimal kastning och i övrigt oklanderliga formsprutningsegenskaper lämpar sig Rynite dessutom väl också för större konstruktionspartier i stil med allehanda — både belastade och obelastade — täckpaneler.
För närvarande har Du Pont redan mer än 20 utvecklingsprogram igång baserade på helt nya hartsalternativ — för exempelvis elektriska, transmissions-, bromssystems- och andra hårt belastade driftmekaniska detaljer.
Dessa exempel är dock bara små axplock bland många dellösningar på det enorma problem personbilen är i den stora petroleumindustriella krisfrågan. Kai Finell
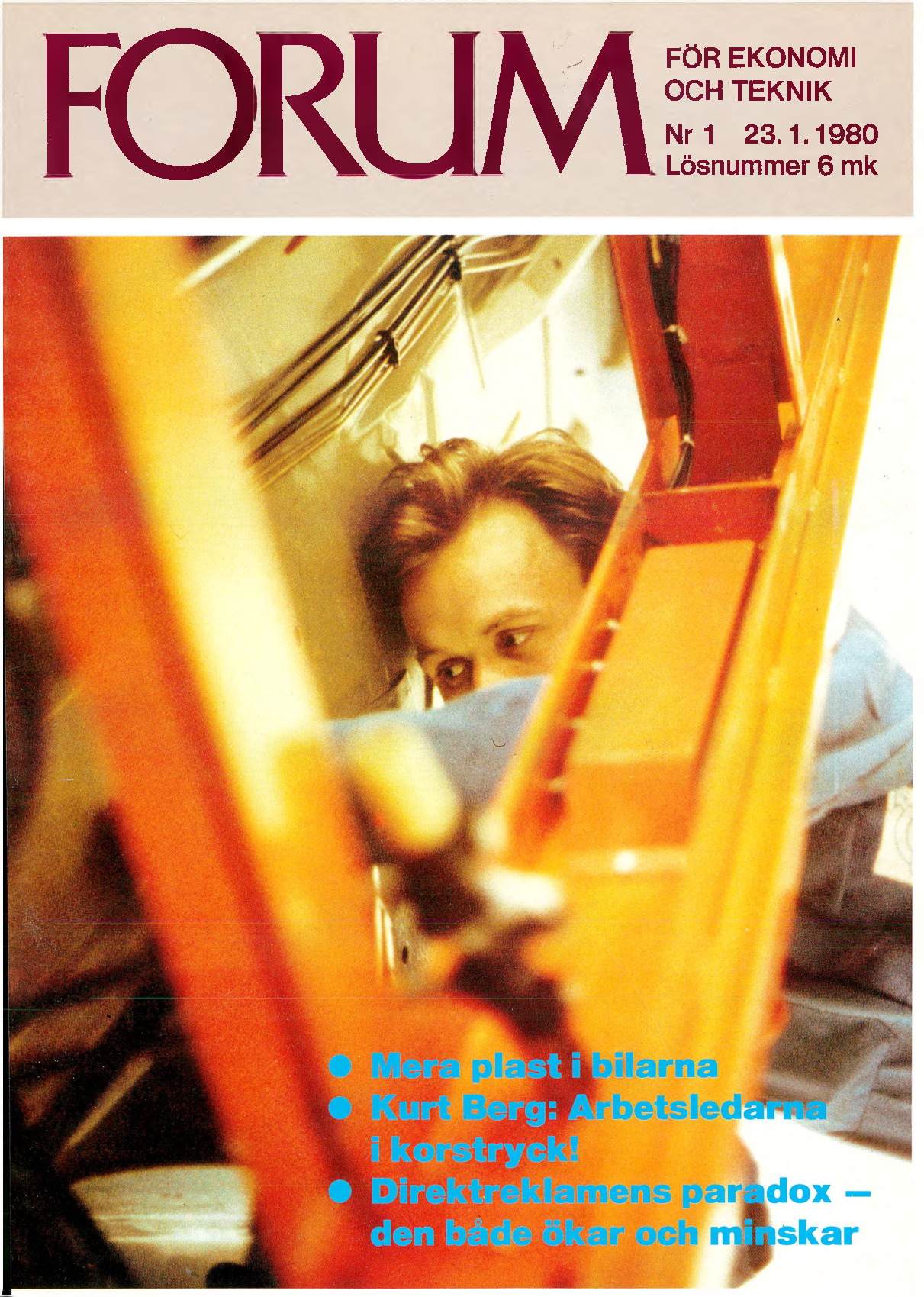